EMI Filters
Switched mode power supplies (SMPS's) typically generate high frequency noise that
must be attenuated. These unwanted electrical signals can pass from the power supply
onto the input power lines. Other electronic equipment sharing the lines may be
subjected to this conducted noise, which can cause errors and possibly even
catastrophic faults in connected equipment. An EMI noise filter inserted at the SMPS
power input (see figure below) can block this type of interference. This diagram shows
a differential noise filter and a common mode noise filter in series. In many cases the
common mode filter is used alone, as it can often eliminate as much as 90% of the unwanted
noise (including some differential mode noise, because even a nearly ideal common mode
choke will exhibit a small differential impedance).
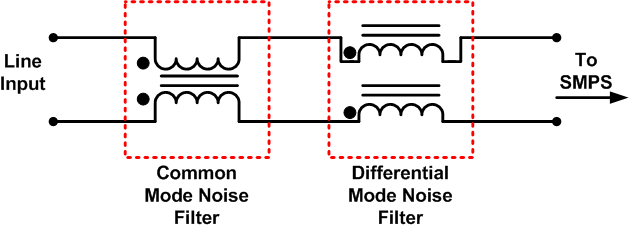
Schematic of an EMI Filter
Common Mode Filters
In a common mode noise (CMN) filter each winding of the inductor is connected in series with one of
the input power lines. The connections and phasing of the inductor windings are such that the
flux created by each winding appears to cancel (actually sums to zero within the core material)
the flux generated by its opposing winding. The insertion impedance of the inductor to the
input power line is therefore negligible.
The two figures below illustrate both the flux generated by the power lines and that induced by
any common mode noise present on the lines. While 'power line' flux sums to zero (often
thought of as 'canceling') because of its opposing nature, the common mode flux is left
unopposed and therefore encounters the high reactive impedance of the core material. This
high impedance offers filtering action against the common mode noise.
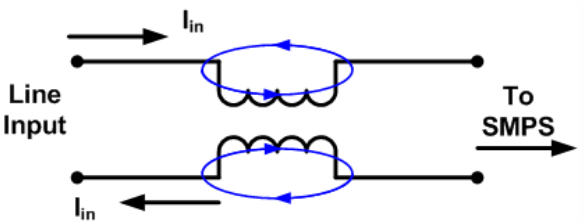
Filter Reaction to Input Line Current
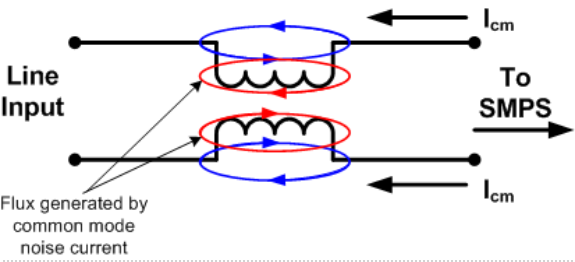
Filter Reaction to Common Mode Noise Current
Current Filter Reaction to Common mode noise toroidal cores are most popular for CMN
filters as they are inexpensive and have very low leakage flux with high CMN
impedance. Toroids may have higher winding costs than bobbin wound shapes such as
EE and pot cores. However, the higher inductance allowed by having no inherent air
gap at a mating surface can add as much as 30% more impedance for the same core
material. It is typical for a non-metallic divider to be inserted between the two
windings for mains isolation, and the wound unit is epoxied or the leads mounted to a
printed circuit header for attaching to a PC board.
An illustration is below. The device is typically called a common mode choke or
common mode inductor.
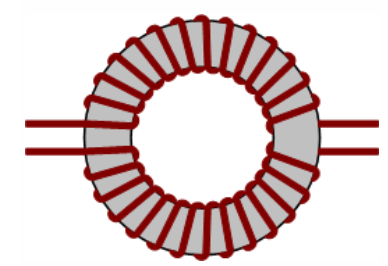
Common Mode Inductor Winding Arrangement
Design Method Summary
The basic parameters needed to select a core for use as an effective common mode
inductor are input line current (I, in ARMS),frequency (f, in Hz),
and series impedance
(Zs, in Ohms). Although many designers specify CMN designs based on inductance
instead of frequency and impedance, these specifications can be regarded as
equivalent to one another (see equations below and Help notes regarding the
software's design modes). The current input, along with an expected current
density, determines the wire size. Conservative current density values
(e.g. 400 A/cm²) imply larger wire sizes that will not significantly heat up.
More aggressive values (800 A/cm² or higher) allow a smaller inductor design,
but with the potential for more heat build-up. The impedance of the inductor is
normally specified as a minimum at a given frequency. This frequency is usually
low enough to allow the (very important) assumption that the inductive reactance,
Xs, supplies essentially all of the impedance. Consequently, the inductance may
be calculated from:
Ls=Xs2πf
the inductance and current known, analytical (such as this design software)
or graphical (as shown below) design tools may be used to select the core size based
on the LI (really LsI ) product, with L in mH and I in Amps.
Both the curves above and the design software use an algorithm that finds a core
size large enough to accommodate the necessary number of turns while maintaining
a 30° arc of free space between the start and stop of both windings.
This will allow enough room for an isolating spacer to be deployed between the
windings. The wire size (AWG) is then calculated using the following equation based
on the current density (Cd) selected.
$$ AWG = -4.31 \ln ( {1.889 I \over C_d } ) $$
To complete the design, the number of turns per winding is determined from
the core's AL value as follows:
$$ N = {L_s 10^6 \over A_L}^{1 \over 2} $$